Wie können Sie den sterilen Flüssigkeitstransfer beschleunigen und dabei die Sterilität erhalten?
Der DPTE-BetaBag® spielt beim Scale-up der Produktion und bei High-Speed-Anwendungen mit Flüssigkeitstransferlösungen eine immer wichtigere Rolle. Er bietet eine Lösung für den aseptischen Flüssigkeitstransfer mit maximaler Sicherheit und Sterilität. Insbesondere bei der Endfiltration und bei Abfüllprozessen muss die Sterilität während des gesamten Vorgangs gewährleistet sein.
Das DPTE®-System basiert auf der Integration einer Alpha- und einer Beta-Komponente. Jede Komponente ist mit einer Tür, einer Verriegelungs- und einer Dichtungsfunktion ausgestattet. DPTE® ist der ursprüngliche Rapid Transfer Port (RTP). In Verbindung mit dem DPTE-BetaBag® bietet er eine Möglichkeit für den aseptischen Transfer von Komponenten in die Abfüllanlage. Der DPTE-BetaBag® wird unter ultrareinen Bedingungen gefertigt. Er kann vorsterilisiert und von den Partnerunternehmen von Getinge vorab mit Schläuchen ausgestattet oder mit Komponenten vorbefüllt werden, um eine einfache Lösung für die Hersteller pharmazeutischer und biopharmazeutischer Produkte zu gewährleisten.
Komplexe Situationen beherrschen
Bei einem so komplizierten Prozess wie der aseptischen Abfüllung zur Herstellung steriler Arzneimittel können eine Reihe von Schwierigkeiten auftreten. Die Qualitätssicherung erfolgt durch eine Kontrolle von Kontaminationen durch Mikroben, Partikel und Pyrogene und ist entscheidend, um die Sicherheit von Medikamenten und Patienten zu gewährleisten.
„Eine der größten Herausforderungen bei der Einführung von Einmalbaugruppen in der Endabfüllung sind Lecks, die zum Verlust der Sterilität führen könnten“, erläutert Catherine Bianchi, Marketing Group Leader, Bioprocess Solutions bei Saint Gobain. In den letzten Phasen des Bioprozesses kommt es auf jeden Tropfen an. Jede Kontamination im Abfüllsystem oder jedes Leck reduziert die Zahl der verfügbaren Dosen. Das kann auch die Bedienersicherheit negativ beeinflussen, insbesondere bei hochpotenten Wirkstoffen oder Antikörper-Wirkstoff-Konjugaten. Wir müssen bei der Endabfüllung beide Aspekte berücksichtigen, innen und außen.“
Ohne einen Transferport würde das Einbringen von Produkten in eine Abfüllanlage eine Sterilisations- oder Dekontaminationsschleuse erfordern – ein zeitaufwändiger Prozess, der eine zusätzliche Validierung erfordert. Gerade beim Flüssigkeitstransfer sind die traditionellen Edelstahlbehälter, die gereinigt, sterilisiert und gewartet werden müssen, umständlich.
Schnellere Markteinführung
Der DPTE-BetaBag® ermöglicht einen deutlich schnelleren Herstellungsprozess und reduziert das Risiko einer Kreuzkontamination. Der DPTE-BetaBag® ist in eine Baugruppe zum Einmalgebrauch integriert, die für schnelle Flüssigkeitstransferanwendungen entwickelt wurde und als vorab sterilisierte Komponente verfügbar ist. Diese Baugruppe zum Einmalgebrauch ermöglicht größere Flexibilität und erleichtert den Wechsel zwischen den Chargen.
Auftragshersteller (CMO), die für verschiedene Unternehmen produzieren, müssen die Produktion schnell von einem Medikament auf ein anderes umstellen. Komponenten für den Einmalgebrauch bieten Vorteile für den schnellen Wechsel und minimieren die Notwendigkeit einer umfangreichen Dekontamination und Reinigung beim Umschalten der Produktion zwischen verschiedenen Produkten.
„Eine schnelle Markteinführung ist das A und O.“ – Chuck Raye, Mobius® Final Fill Product Manager bei Merck. „Früher, als eine Abfüllanlage komplett aus Edelstahl-Komponenten bestand, war der Hersteller der Abfüllanlage für den gesamten Prozess zuständig, auch für den Flüssigkeitsstrom. Mit modernen Komponenten für den Einmalgebrauch können die Anlagenhersteller jetzt das Design so anpassen, dass mehrere Produkte oder mehrere Füllformate – wie Fläschchen, Spritzen oder Kartuschen – auf einer Abfüllanlage verarbeitet werden können. Baugruppen für den Einmalgebrauch ermöglichen einen schnelleren Transfer, ein geringeres Risiko der Kreuzkontamination, den Wegfall von Reinigungs- und Sterilisationsschritten und eine kürzere Rüstzeit.“
Einer der „Fill & Finish“-Kunden von Merck konnte seine Gesamtverarbeitungszeit, vom Einrichten und Reinigen bis zum Abfüllen und Verpacken, von 36 Stunden auf 12 Stunden reduzieren. Das Unternehmen konnte seine CO₂-Bilanz verbessern und seine Kapazität um 40 % erhöhen. [1]
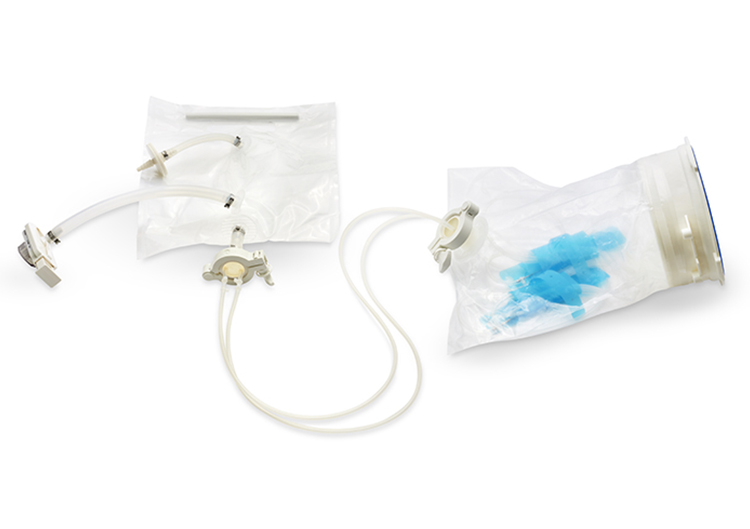
Merck SU Abfüllanlage mit DPTE-BetaBag®
Sicherheit an erster Stelle
Da es sich um einen kritischen Prozessschritt handelt, muss die Abfüllung in einer besonders reinen und kontrollierten Umgebung erfolgen. Um diese Sicherheit zu gewährleisten, stellt Getinge den DPTE-BetaBag® in Reinräumen der Klasse ISO 5 oder ISO 7 her und validiert ihn dann am Produktionsstandort des Partnerunternehmens erneut. „Getinge liefert uns den DPTE-BetaBag® und wir modifizieren den Beutel dann, indem wir Flüssigkeitsanschlüsse anschweißen, die es uns ermöglichen, die Schlauchleitungen zu montieren und einen sterilen Durchflussweg von außen in den DPTE-BetaBag® zu schaffen“, erklärt Chuck Raye. Die Herstellungs- und Sterilitätsprozesse von Merck stellen die endgültige integrierte Lösung des DPTE-BetaBag® und der Komponenten sicher – eine sterile Baugruppe für den Einmalgebrauch, die in eine Isolator-Abfüllanlage integriert werden kann.
Der DPTE-BetaBag® hilft uns, unsere Abfüllkomponenten für den Einmalgebrauch sicher von außen in einen Isolator zu transferieren, ohne dass das Risiko einer Kontamination der Füllnadeln oder der Schläuche besteht.
„Die DPTE®-Technologie ist das Bindeglied“, sagt Catherine Bianchi, Marketing Group Leader Bioprocess Solutions bei Saint-Gobob.
„Sie ist die Schlüsselkomponente, die es uns ermöglicht, unsere Baugruppe in den endgültigen Abfüllprozess und in den Isolator zu bringen. Diese Technologie sorgt für die Sicherheit der Bediener und schützt gleichzeitig das Produkt, was wiederum die Patienten schützt“, fügt Bianchi hinzu.
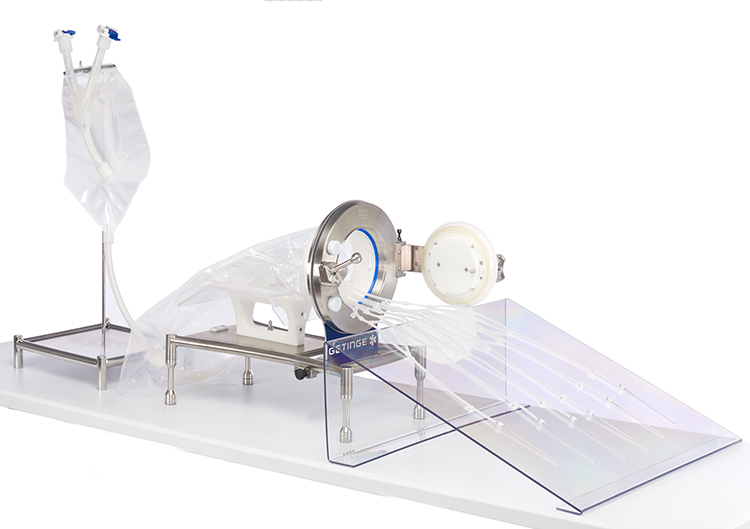
Nach Kundenspezifikation gefertigte Anlage für die Endabfüllung bei Saint-Gobain Life Sciences
Ein wachsender Markt
In den letzten Jahren ist der Markt für Einmalprodukte für den Flüssigkeitstransfer jährlich um ca. 25 % gewachsen, vor allem aufgrund der steigenden Produktion von Biologika. Es wird erwartet, dass sich der Trend hin zu Komponenten für den Einmalgebrauch fortsetzt, und Chuck Raye ist überzeugt, dass sich hier für alle Mitarbeiter die Gelegenheit bietet, enger zusammenzuarbeiten und innovative neue Baugruppen zu entwickeln. „Zahlreiche Kunden und Lieferanten für Produkte zum Einmalgebrauch suchen nach Möglichkeiten, die Designs und Verfahren zur Implementierung zu standardisieren. Das dürfte eine große Herausforderung werden, aber die Branche muss diese Entwicklung unterstützen, um der wachsenden Nachfrage gerecht zu werden.“
Produkte für den Einmalgebrauch sind wegen ihrer vielen Qualitäts- und Prozessvorteile auf dem Vormarsch. Sie ermöglichen ein höheres Maß an Flexibilität und reduzieren gleichzeitig den Kapitaleinsatz, die Arbeitskosten und sogar den Wasser- und Energieverbrauch.
Einmalprodukte fördern auch den Einsatz von Multi-Produkt-Anlagen, die mit kleineren Chargen arbeiten. Ein Trend, der sich gut mit neuartigen Therapien wie Orphan Drugs oder Gentherapien für kleinere Patientenpopulationen ergänzt.
Partnerschaften für mehr Innovationen
Stabile Partnerschaften zwischen Getinge – dem Hersteller des DPTE-BetaBag® – und den Lieferanten der gebrauchsfertigen, vorgefüllten Lösungen sind ein wichtiger Teil dieser Erfolgsgeschichte. Anneke Evers, Senior Director Sales and Market Support for DPTE® Sterile Transfer bei Getinge, schätzt das unterschiedliche Fachwissen, das jede Partei mitbringt. „Für mich ist es großartig, Spezialistin für den DPTE-BetaBag® zu sein, denn unser Wissen über den aseptischen Transfer liefert in Kombination mit dem spezifischen Know-how unserer Partner für den Flüssigkeitstransfer ein innovatives Ergebnis.“
Wir waren auf der Suche nach einem Partner, der über eine starke Branchenpräsenz und eine bewährte Technologie verfügt, und Getinge ist seit Jahrzehnten der Branchenführer bei Isolator-Transferanwendungen.
Catherine Bianchi stimmt zu: „Wir wollen Zuverlässigkeit, Produktqualität, schnellen technischen Support und Fachwissen über die Endabfüllung. Und Getinge ist ein Unternehmen mit einer langen Tradition und einem guten Ruf für ausgezeichnete Qualität.“
Um die guten Beziehungen aufrechtzuerhalten und die Branche weiter voranzubringen, tauscht sich Getinge regelmäßig mit seinen Partnern aus, um sowohl über Probleme als auch über Trends zu sprechen. „Wir besuchen gegenseitig unsere Werke, um uns ein Bild von den Möglichkeiten und Neuentwicklungen zu machen, und wir führen auch betriebswirtschaftliche Prüfungen durch, um Trends zu analysieren und gemeinsam die zukünftigen Anforderungen zu erfüllen“, sagt Raye. „Zu wissen, dass wir einen Lieferanten und Partner haben, der unsere Anforderungen erfüllen kann, ist entscheidend für den langfristigen Erfolg von Lösungen für den Einmalgebrauch.“
Anneke Evers freut sich ebenfalls auf die Zukunft des DPTE-BetaBag® und fügt hinzu, dass noch in diesem Jahr eine neue Produktionsstätte in den USA eröffnet wird. „So können wir die Kosten für Transport und Zölle auf dem nordamerikanischen Markt reduzieren und gleichzeitig unseren ökologischen Fußabdruck verkleinern“, sagt sie. Wir müssen uns gemeinsam für eine nachhaltigere Zukunft einsetzen. Aus diesem Grund setzt Getinge auch auf Innovationen im Bereich der Produktnachhaltigkeit und des Abfallmanagements.“
Getinge engagiert sich für Partnerschaften und Kooperationen, um Innovationen zu entwickeln und eine flexible, optimierte und kosteneffiziente Produktion sowie ein Höchstmaß an Prozess- und Patientensicherheit zu gewährleisten.