An automated bioreactor solution tailored for the next generation of science
At the Delft University of Technology in the Netherlands, professors and PhD students needed a new solution for evolutionary engineering – to improve the study of genetically engineered cells in the pursuit of replacing more petrochemicals with plant-based materials. This called for a robust, flexible, and automated bioreactor setup tailored to meet the specific challenges related to evolution studies.
Dr. Ir. Robert Mans, Assistant Professor at the Department of Biotechnology, explains why their scientific work in the laboratory needed more automation: “The challenge is that cells are extremely complex and it’s impossible to always fully understand what happens inside them. Sometimes, genetically engineered cells behave as intended — and other times, they become sick and grow slowly. Our way of optimizing this is by using evolution. Letting the cells evolve to become healthier and grow faster. And this requires extremely reliable and sterile equipment,” says Dr. Mans. “So, we needed a more automated solution to allow for a closed operation without having to open anything during the month-long processes.”
Sophie de Valk, one of the PhD students under the supervision of Dr. Mans, explains how the previous setup made her work with the genetic engineering of yeast more complex and time intensive: “We used to be relatively limited in terms of how we could automate evolutions. We had to change the medium by hand –always with a risk of contamination and potential setbacks. So, we definitely felt the need for precise process control and the ability to set up even more complex system scripts.”
With a thorough understanding of their specific requirements, the team at Delft University of Technology needed a partner that could both provide the necessary expertise and invest the time in designing a nonstandard solution. “From a theoretical point of view, we knew exactly what we wanted. But we needed someone to actually realize our vision. Someone who could create and implement a solution with all the flexibility that is required to perform our experiments,” explains Dr. Mans.
We were already familiar with Getinge and know their system to be very robust and reliable. But I think that the biggest difference for us was that Getinge is so open to creating tailored solutions. To partner and co-develop a tailored setup instead of an off-the-shelf option.
A complex bioreactor engineered for simplicity
Rowin Timmermans, a Sr. Application Specialist with 12 years of experience with Applikon solutions, was a part of the team that took up the challenge. He immediately knew that the complex nature of the task called for process-control scripts in the customer’s SCADA software that could significantly reduce the number of manual interventions. “We needed to automate two types of long-duration processes: a repeated batch process and a chemostat or accelerostat process. Normally, both would require a lot of manual interventions. So, the main challenge was to combine the data from the TU Delft research team’s own offgas analyzer devices with all the process data from the Applikon ez-Control system — and then use this online data to automatically control the repeated batch and chemostat or accelerostat processes in the desired way,” Timmermans explains.
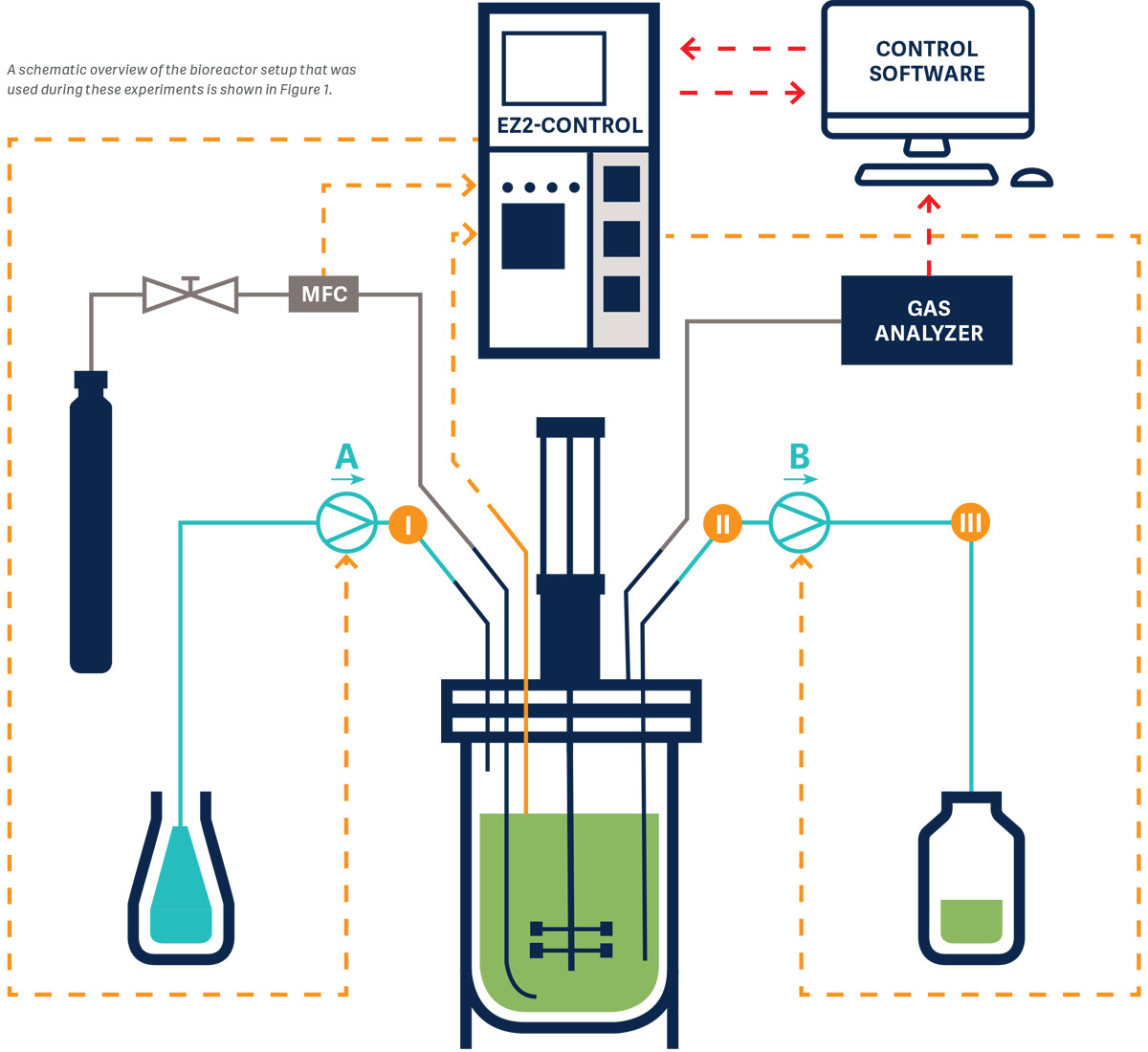
Timmermans was in charge of writing the scripts to control everything that happens in the fermentation process. This was based on a very close collaboration with the team from the Department of Biotechnology at Delft University of Technology. “My primary role was to program the scripts in Lucullus®, the software solution provided by Getinge, to achieve the process automation. During our collaboration, I visited the university several times to run tests together. I think that this way of working together — with frequent and constructive feedback — is the key to success. It’s the only way to fully understand a specific need and come up with a solution that is tailored to the customer’s exact needs,” Timmermans concludes.
When asked about the most challenging task during the process, he says: “One of the greatest challenges was to grasp the way the chemostat, and especially the accelerostat, principles work — and the complexity of some of the criteria we programmed in scripts to move from one process step to the next.”
Just like Timmermans, Dr. Mans and his team found the close collaboration valuable and part of the reason why the whole process went relatively swiftly. Dr. Mans shares his thoughts on the collaborative process: “I would have predicted more hiccups than we encountered. It was pretty much checking boxes, which actually surprised me because it’s a quite complicated system to set up. In a relatively short time – based on a period of trial and error – we managed to get to an end result that does everything we wanted from the system.”
Customized benefits – designed for general use
Dr. Mans’ PhD student, Sophie de Valk, points to some of the highlights and benefits of the new system from her point of view:
I like how easily you can monitor many things going on in the reactor online. Previously, you always had to export the data first and then plot it in Excel. Now, you don’t have to stare at your reactor all the time to know that everything is going smoothly. You can see that fairly easily in three clicks — even when working from home.
Apart from having instant access to online monitoring from anywhere, de Valk also mentions the simplicity and flexibility that characterizes the new automated evolution system: “Now it’s really easy to set up a quite complicated automation script. You don’t need to spend weeks with the students building everything from the bottom. Also, I’ve had cases where we wanted to tweak some parameters during the evolutions in real-time. Now we can do that because it’s super easy to track signals online and see how everything is going and growing. And based on the monitoring data, we can adjust the pH, sparge more air, or make any adjustments needed.”
In the end, both the TU Delft research team and those involved from Getinge were so pleased with the result that they hosted a joint webinar to provide global outreach and share both their learnings from the process and the possibilities of the cutting-edge automated bioreactor system — which, even though it was highly tailored, was intended for general use from the very beginning. Hence, Dr. Mans and his team also wrote a scientific publication to make the knowledge accessible to the global academic community.
Bringing science to life – not just from the sideline
On a final note, we asked Sophie de Valk and Dr. Robert Mans from Delft University of Technology about their biggest motivational drivers for working with Life Science.
Part of it is driven by climate change. Knowing that you can actually contribute and give an alternative to the fossil-based industry and become more plantbased. It feels really good. Also, the life-science field is still developing very fast. There’s really cutting-edge innovation going on at the moment and it’s really cool to be a part of that.
Dr. Mans also points to taking an active part in the fight against climate change as a huge motivational driver. “As a society and a world population, there are big steps that we need to take in order to both limit and reduce the effect of climate change. Knowing that we are contributing simply by doing what we do every day — for me, that’s a really big motivation. Otherwise, I would have felt like I was sitting on the sideline. I know that with my job, I am part of the solution. I’m not sitting on the sideline. I’m actually involved and, hopefully, making a difference,” he concludes.
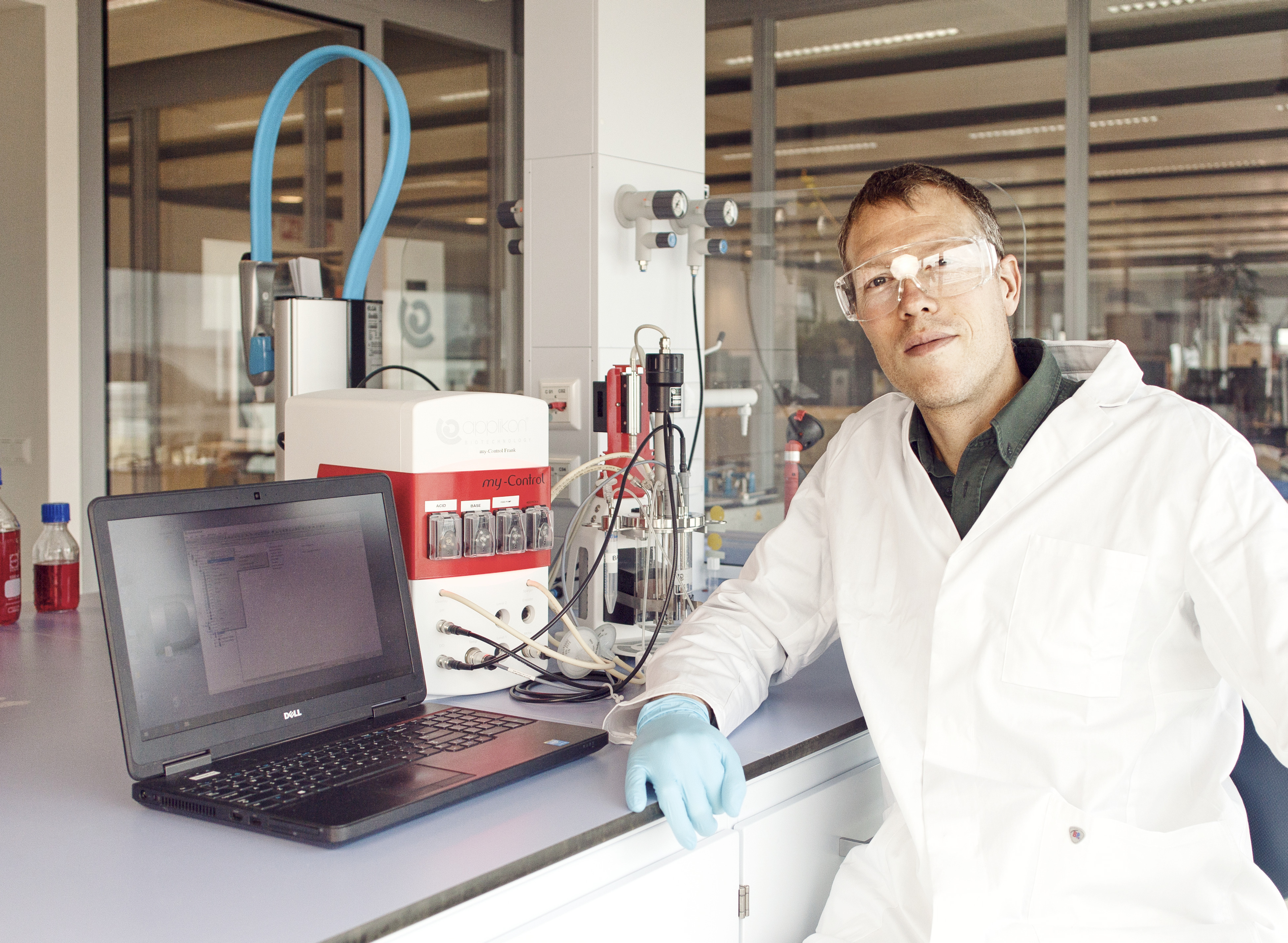
One of the greatest challenges was to grasp the way the chemostat, and especially the accelerostat, principles work — and the complexity of some of the criteria we programmed in scripts to move from one process step to the next.