DPTE® 60-year anniversary
For six decades, DPTE® technology has been keeping people and products safe from potentially harmful materials or contaminants. Today, DPTE® is an essential part of pharmaceutical research and manufacturing – because ultra-clean production demands ultra-clean transfer methods.
From nuclear containment to pharmaceutical production
The origins of the DPTE® rapid transfer port can be traced all the way back to the dawn of the nuclear age in the 1940s. The more researchers and engineers worked with radioactive material, the more they noticed its deadly effects. To keep people safe, they needed a containment solution that was 100% leaktight.
In the 1960s, La Calhene (part of Getinge since 2005) began working with the French Atomic Energy Board (CEA) to develop remote handling systems, special containers for nuclear waste, and the world’s first mechanical containment system – DPTE®, which stands for Double Porte de Transfert Etanche (or, in English: Double Door for Leak-tight Transfer). Today this system is also known as a Rapid Transfer Port or RTP.
The first DPTE® system was introduced in 1963 and for 30 years, La Calhene was the only manufacturer of this type of leaktight port with a secure lock that eliminates the risk of human error. The team also quickly realized that the DPTE® system was ideally suited for use in other industries where containment and protection are critical. In fact, by the 1980s it was clear that DPTE® was going to play a major role in the future of medicines and vaccines.
DPTE®: a game-changer in pharmaceutical production
The first pharmaceutical manufacturing unit within a DPTE® isolator system was developed by La Calhene in 1978 for an Italian biopharmaceutical company. This powder-filling operation unit had a purpose very different from the nuclear industry: protecting patients by also protecting the inside of the barrier system. With DPTE®, materials for medicines could now be transferred in and out of an aseptic environment without breaking sterility.
The introduction of the DPTE® rapid transfer port led to a revolution in pharmaceutical research and in the manufacturing and production of medicine – particularly injectable medicines. By the 1990s filling lines were designed to create a closed system with DPTE®, ensuring full protection of the product within the sterile process as well as the people in the environment.
Innovation and future potential
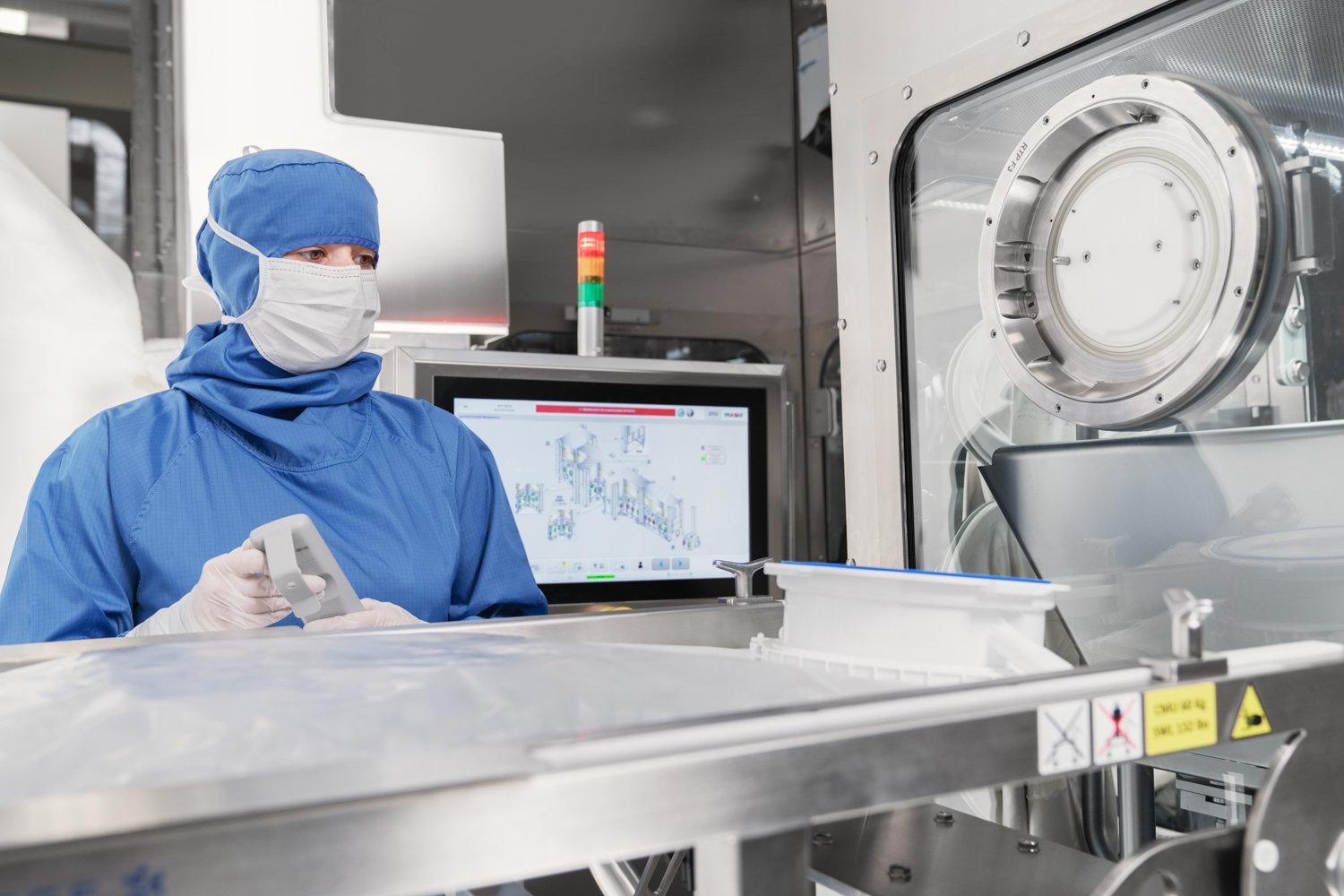
Over the years, DPTE® innovation has led to a number of important advancements, particularly the DPTE-BetaBag®. The single-use, ready-to-use DPTE-BetaBag® was introduced to enhance patient safety by reducing the risk of contamination even further. Each DPTE-BetaBag® is manufactured in ultra-clean conditions (ISO 7 and ISO 5) and can be pre-sterilized and even supplied pre-filled with components from manufacturers, eliminating the need for special processing departments.
As the need for isolation technology has increased, so has the need for better transfer technology. Due to GMP Annex 1 recommendations, most pharmaceutical manufacturers now need a completely confined production area with a DPTE® port to introduce materials.
The pharmaceutical industry is also moving towards more integrated, automated, and gloveless production systems. A rapid transfer port that is operated from outside the filling line, the new DPTE®-EXO ensures a secure, reliable, and automated transfer solution. It was designed to significantly reduce the risk of contamination with gloveless transfers and provide enhanced traceability and data analysis thanks to full connectivity.
The trend toward more automation is set to continue, along with the proliferation of more smaller-scale applications and smaller isolators due to new vaccines, liquid biopharmaceuticals, and cell and gene therapies. With more and more applications benefiting from DPTE®, the application of DPTE® technology may one day even extend out into our solar system where it could be used to maintain sterile conditions for samples on a mission to Mars.
Meeting today’s challenges with 60 years of experience
At Getinge, we have the experience, quality, reliability, and technology to meet the needs of today’s innovative research facilities and pharmaceutical manufacturers. Our multiple production sites have the capacity to deliver our full DPTE® portfolio – including the largest DPTE-BetaBag® range on the market – to customers around the world.
Since 1963, DPTE® has been ensuring the highest level of safety for processes and people – and we are committed to working with our partners and customers to ensure flexible, cost-effective production no matter the application.