Seguire le buone pratiche può migliorare i risultati nelle linee di riempimento asettiche
Procedure adeguate possono ridurre il rischio di non conformità durante il ciclo in autoclave di tappi e chiusure farmaceutiche
L'essere umano ha una naturale propensione a superare i limiti di qualsiasi sistema. Riempiamo eccessivamente i bagagli prima di un viaggio o le buste della spesa al supermercato. A volte però meno è meglio, soprattutto quando si tratta dei componenti sterili utilizzati in una linea di riempimento asettica.
L'importanza della sterilizzazione in autoclave
La sterilizzazione in autoclave è fondamentale per prevenire la contaminazione e una tecnica adeguata è indispensabile per il successo. Il processo utilizza il calore del vapore per distruggere qualunque forma di vita microbica, evitando l'introduzione di microrganismi estranei in un ambiente sterile. Il vapore utilizzato nel processo di sterilizzazione è un trattamento molto stressante per le materie prime plastiche, che devono essere trattate con cura.
La sacca flessibile DPTE-BetaBag® è da tempo considerata la soluzione ottimale per il trasferimento sicuro, rapido e privo di contaminazione di componenti quali cappucci, tappi o pistoni destinati alle linee di riempimento asettiche. Pratiche non ottimali possono tuttavia compromettere il buon esito del processo.
La non conformità può comportare la presenza di microrganismi capaci di mettere a rischio la produzione. Quando la sterilizzazione terminale non è possibile (perché il prodotto è sensibile al processo di sterilizzazione), è necessario garantire la sterilità in ogni fase del processo di riempimento asettico. Il modo migliore per garantire questa sterilità consiste nel prevenire ogni forma di ingresso microbico.
Sterilizzazione in contenitori e sacche DPTE-BetaBag®
Per garantire risultati di processo ottimali nella sterilizzazione di tappi in gomma o carichi porosi all'interno di una sacca DPTE-BetaBag® sono necessari alcuni specifici accorgimenti. "Puntiamo all'efficienza sia per quanto riguarda il risultato della sterilizzazione, sia per il contenuto di umidità residua all'interno della sacca", sottolinea Joakim Larsson, Product Line Manager di Getinge, divisione Sterilizzatori.
Garanzia di sterilità/rimozione dell'aria/penetrazione del vapore
Per una corretta sterilizzazione, sono fondamentali la rimozione dell'aria e la penetrazione del vapore. Il lato in Tyvek della sacca agisce come filtro, creando un ritardo di pressione tra l'interno e l'esterno della sacca. Per garantire una corretta rimozione dell'aria prima della sterilizzazione, è consigliabile rallentare la velocità di creazione del vuoto. La creazione di un vuoto progressivo controllato in cui il livello di vuoto è un parametro regolabile consente di ottimizzare ogni carico.
Il secondo metodo consiste nell'inserire un periodo di mantenimento del pre-vuoto che permette di equalizzare la pressione al livello inferiore di vuoto prima di introdurre il vapore, che aumenterà di nuovo la pressione. In questo modo si riduce al minimo il rischio che la differenza di pressione causi rigonfiamenti che possono danneggiare la sacca.
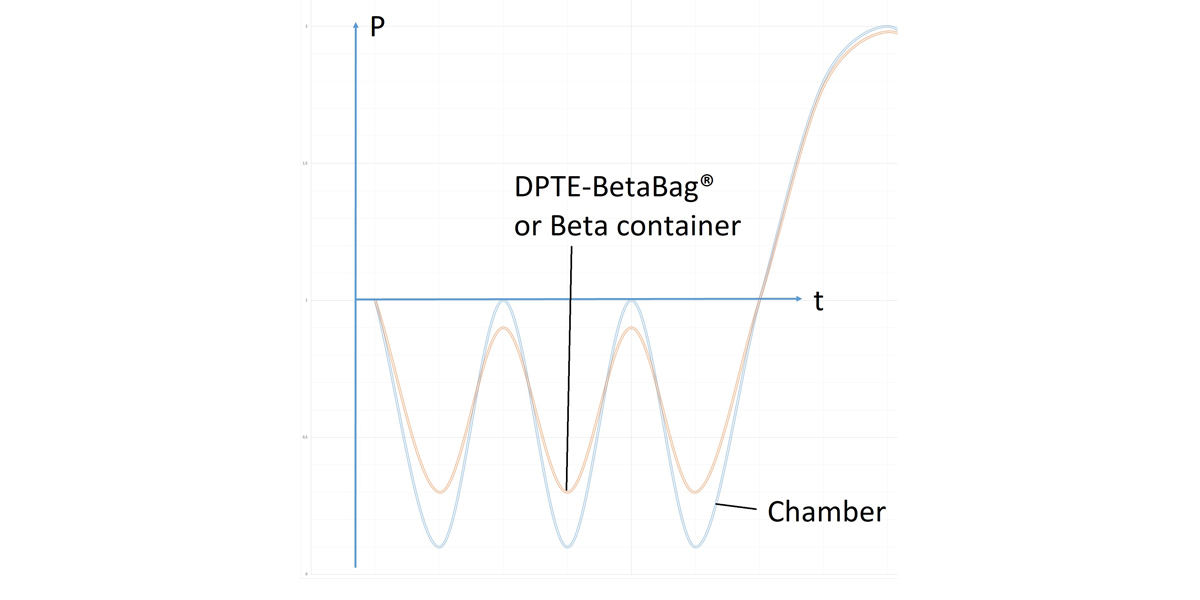
Essiccazione del carico
Durante il riscaldamento mediante vapore, l'aumento di temperatura genera condensa. La quantità di condensa è proporzionale all'aumento della temperatura e al peso del carico.
Se il peso del carico è costante, la condensa può essere ridotta utilizzando il preriscaldamento a secco. Il carico può essere riscaldato prima che il vapore venga iniettato direttamente nella camera e prima della rimozione dell'aria.
I carichi devono essere riscaldati a circa 100 °C, portandoli dalla temperatura ambiente al plateau di sterilizzazione (20° - 121 °C). Il preriscaldamento a 70 °C precedente all'iniezione diretta del vapore dimezza la quantità di condensa.
È inoltre possibile erogare impulsi di essiccazione ripetuti dopo aver raggiunto il plateau di sterilizzazione, attraverso impulsi di vuoto alternati a impulsi di sovrapressione. Gli impulsi di vuoto aspirano l'aria umida dalla sacca, mentre quelli di sovrapressione assicurano che l'aria secca penetri attraverso il lato in Tyvek della sacca e raggiunga i tappi.
Ogni impulso di sovrapressione trasferisce l'umidità dal carico all'aria grazie alla spinta di compensazione, che tende a creare un livello equilibrato di umidità.
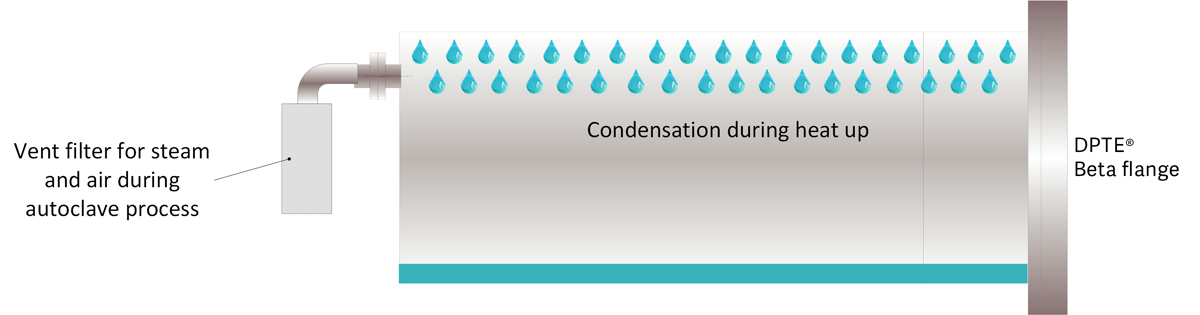
Evitare il rischio del "fattore umano"
"L'esperienza acquisita negli anni ha dimostrato che il fattore umano è spesso la causa principale di sterilizzazioni non conformi", ha affermato Cyril Mounier, Specialista delle applicazioni farmaceutiche di Getinge. "L'innata tendenza a sovraccaricare le cose può incidere in modo negativo sulla riuscita del processo di sterilizzazione".
Puntando a ridurre i costi complessivi dei clienti, Getinge ha identificato quelle pratiche ad alto rischio che spesso provocano la mancata conformità del processo di sterilizzazione in autoclave. "Nel 2019 abbiamo condotto una serie di test presso lo stabilimento Getinge La Calhène di Vendôme, in Francia", ha spiegato Anne-Claude Gilbert, R&D Plastics Engineer di Getinge.
Come leader di mercato nelle soluzioni di trasferimento asettico e creatore della tecnologia DPTE®, Getinge è impegnata nell'individuazione costante dei parametri che possono influenzare le prestazioni delle sacche DPTE-BetaBag® Tyvek[1],[2]. Tali sacche vengono utilizzate per sterilizzare in autoclave i componenti e caricarli direttamente in una linea di riempimento asettica.
"Abbiamo esaminato sia i parametri generali del processo sia gli elementi specifici delle fasi di sterilizzazione ed asciugatura", ha affermato Anne-Claude.
È apparso evidente che per ottenere il miglior risultato in termini di resistenza della tenuta e integrità, le sacche DPTE-BetaBag® Tyvek devono essere riempite fino ad un livello predeterminato e sottoposte a uno specifico ciclo in autoclave.
Cosa si intende con DPTE®?
DPTE è l'acronimo francese di Double Porte pour Transfert Etanche (Doppia porta per trasferimenti ermetici). Il sistema è costituito da unità "alfa" e "beta" interbloccate, con la parte alfa montata sulla parete di contenimento e la parte beta fissata a un contenitore o a una sacca. La tecnologia, sviluppata da Getinge La Calhène più di 50 anni fa, è ancora lo standard di riferimento per il trasferimento asettico.
La sacca DPTE-BetaBag® Tyvek è un dispositivo che combina la parte DPTE® Beta e una sacca costituita da due pellicole saldate insieme; un lato è in Tyvek e l'altro è in polietilene ad alta densità (HDPE). Le sacche contengono componenti, come cappucci, tappi o pistoni, per la sterilizzazione in autoclave e il trasferimento privo di contaminazione in una zona asettica.
Il costo della non conformità
"Le pratiche non conformi di sterilizzazione in autoclave possono determinare costi significativi, sia in termini di errori di produzione, causati dall'impatto dell'ingresso microbico, sia in termini di costi operativi associati allo smaltimento dei componenti interessati e alla sterilizzazione di nuovi componenti", ha affermato Cyril.
Identificando gli elementi di processo a maggior rischio e definendo buone pratiche per il successo, Getinge ha cercato di migliorare i risultati e ridurre i costi associati alla risterilizzazione o alla contaminazione.
Identificazione dei parametri di processo più importanti
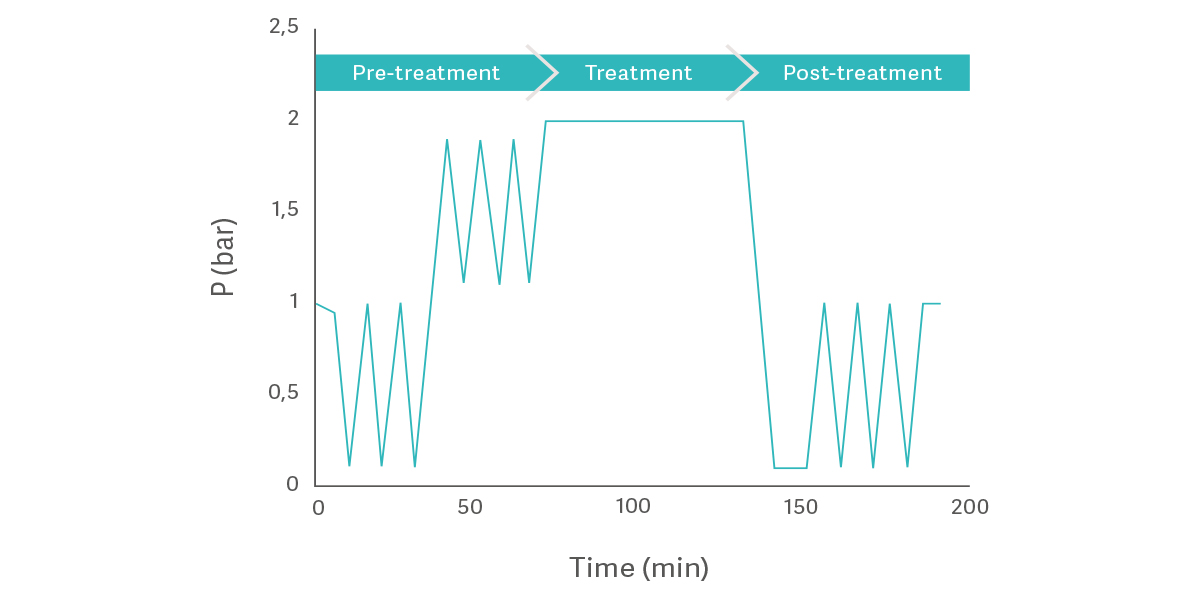
Getinge ha condotto due programmi di test completi per l'analisi di specifici parametri nel processo di sterilizzazione in autoclave 1,2. Questi test hanno analizzato sei parametri in tre categorie principali: parametri generali di processo, parametri di sterilizzazione e parametri di asciugatura.
L'analisi dei parametri generali di processo ha esaminato gli elementi di base del processo e come questi contribuiscono alla sua riuscita complessiva.
- Quanto sono piene le sacche?
- Come sono posizionate?
I parametri di sterilizzazione includevano tempo e temperatura.
- Un tempo di sterilizzazione più lungo compromette l'integrità della sacca?
- Le alte temperature riducono le prestazioni della sacca?
La fase di asciugatura presenta problematiche esclusive.
- La rampa del vuoto — la velocità di gonfiaggio e sgonfiaggio della sacca durante il ciclo di sterilizzazione — incide sulle prestazioni della sacca?
- In che modo gli impulsi incidono sull'integrità della sacca?
Un'analisi dimensionale ha valutato il modo in cui la sacca è stata influenzata dalle variazioni dei sei parametri. Dopo ogni ciclo, ogni sacca è stata misurata e testata per verificarne l'integrità; poiché non tutte le sacche hanno subito danni visibili, sono stati eseguiti test approfonditi avvalendosi del metodo a base di blu di metilene[3]. Il blu di metilene è un test diffuso, impiegato per identificare la presenza di difetti del canale — attraverso la perdita di colorante (Metodo di test standard ASTM F1929 per il rilevamento di perdite di tenuta in imballaggi medicali porosi mediante penetrazione del colorante) — che potrebbero consentire l'ingresso di contaminanti microbici.
Durante ogni ciclo in autoclave
La sacca si gonfia e si sgonfia diverse volte, in funzione delle variazioni di pressione all'interno dello sterilizzatore. Di fatto, l'equilibrio tra la pressione nell'autoclave e quella nella sacca DPTE-BetaBag® non viene raggiunto immediatamente. Durante la variazione di pressione nella camera, si crea una differenza di pressione tra l'autoclave e la sacca. Ogni diminuzione di pressione gonfia la sacca; ogni aumento di pressione la sgonfia.
"I test hanno mostrato una correlazione tra maggiore deformazione della sacca e rischio più elevato di non conformità", ha affermato Anne-Claude.
La ricerca ha concluso che il tempo del ciclo di sterilizzazione e il numero di impulsi post-trattamento non incidono sulla deformazione o sull'integrità della sacca. Tuttavia, le variazioni di contenuto, posizione, temperatura e rampa di vuoto hanno un impatto misurabile sui risultati. Un'ulteriore analisi di questi quattro parametri ha consentito di elaborare le buone pratiche di lavorazione.
Buone pratiche per una sterilizzazione in autoclave efficace
Controllando i quattro fattori relativi a capacità, posizione, temperatura e rampa del vuoto, è possibile ottenere risultati ottimali.
Capacità: Evitare il sovraccarico
"Proprio come una valigia troppo piena, il sovraccarico di una sacca DPTE-BetaBag® Tyvek può incidere sull'integrità strutturale e provocare danni alla sacca", spiega Cyril.
Getinge consiglia di prestare attenzione alla capacità della sacca, per evitarne il sovraccarico. I parametri di riempimento massimi sono indicati di seguito:
- Carico di 8 litri per la sacca doppia in Tyvek DPTE-BetaBag® da 10 litri
- Carico di 13 litri per la sacca singola in Tyvek DPTE-BetaBag® da 23 litri
- Carico di 18 litri per la sacca doppia in Tyvek DPTE-BetaBag® da 25 litri
Posizione: La posizione in piano è la migliore e consente di avvicinare tra loro i ripiani di carico
Come si può vedere dall'immagine 4 (disponibile nel white paper), queste sacche hanno due lati nettamente diversi. Il lato in Tyvek è piatto, mentre la parte DPTE® Beta si trova sul lato in HDPE (polietilene ad alta densità). La ricerca ha evidenziato la necessità di poggiare sempre la sacca sul lato piatto in Tyvek, per minimizzare la sollecitazione del materiale. Se viene posizionata con il lato DPTE® rivolto verso il basso, con l'intenzione di facilitare la "respirazione" attraverso lo strato in Tyvek, la sacca non può appiattirsi; ciò esercita una sollecitazione aggiuntiva e inutile sul materiale e aumenta il rischio di non conformità. La ricerca ha mostrato anche che non è necessario che il lato in Tyvek sia in alto per facilitare lo scambio d'aria.
Il limite creato dal ripiano superiore mentre la sacca si gonfia, durante la fase di vuoto, non incide negativamente sull'integrità della sacca stessa. È possibile ridurre la distanza tra i ripiani fino a 15 cm, per alloggiare più sacche e massimizzare la produttività.
Temperatura: Intervallo ideale da 121 °C a 123 °C
L'analisi dimensionale ha rivelato che temperature di 125 °C e superiori influenzano negativamente l'integrità strutturale e la funzionalità della sacca. Tuttavia, temperature pari a 121 °C, 122 °C, 123 °C e 124 °C sono sufficienti ad assicurare una sterilizzazione efficace (in relazione al tempo di esposizione), ma non così elevate da provocare danni alla sacca.
Temperature che rientrano all'interno di questo intervallo di 3 °C hanno prodotto i risultati previsti, riducendo al minimo il rischio di danni all'integrità della sacca e la conseguente contaminazione dei componenti.
Rampa del vuoto: Ridurre al minimo le deformazioni della sacca
La fase di vuoto in autoclave ha diverse funzioni: rimuovere forzatamente l'aria per garantire che il vapore raggiunga ogni angolo di ogni componente durante la fase di pre-trattamento, rimuovere il vapore e asciugare i componenti durante la fase di asciugatura. Durante un ciclo in autoclave, la sacca si gonfia e si sgonfia ripetutamente, in funzione della variazione di pressione della camera.
L'analisi dimensionale della sacca ha dimostrato che a una maggiore rampa del vuoto corrisponde un allungamento più elevato della sacca; la pressione positiva e quella negativa causano una variazione più ampia della forma della sacca.
Maggiore è l'allungamento, più alto è il rischio di danneggiamento della sacca dovuto alla rottura della pellicola. Poiché il rischio di cedimento strutturale aumenta oltre i 0,5 bar/min, è consigliabile mantenere la pressione al di sotto di tale livello.
Seguire le buone pratiche porta a risultati migliori
È possibile ridurre il rischio di deterioramento della sacca DPTE-BetaBag® Tyvek seguendo le buone pratiche di carico e di autoclavaggio. L'impianto ottiene così un risparmio in denaro, altrimenti sprecato con cicli non conformi.
- Non sovraccaricare la sacca oltre i limiti indicati dal produttore
- Posizionare la sacca in piano, sul lato in Tyvek
- Mantenere temperature massime tra 121 °C e 123°C
- Impostare il valore minimo accettabile per la rampa del vuoto per evitare la deformazione della sacca
Seguendo queste quattro semplici indicazioni, la vostra organizzazione può garantire la riuscita della sterilizzazione e mantenere la sterilità fino al trasferimento.
Scarica il white paper qui:
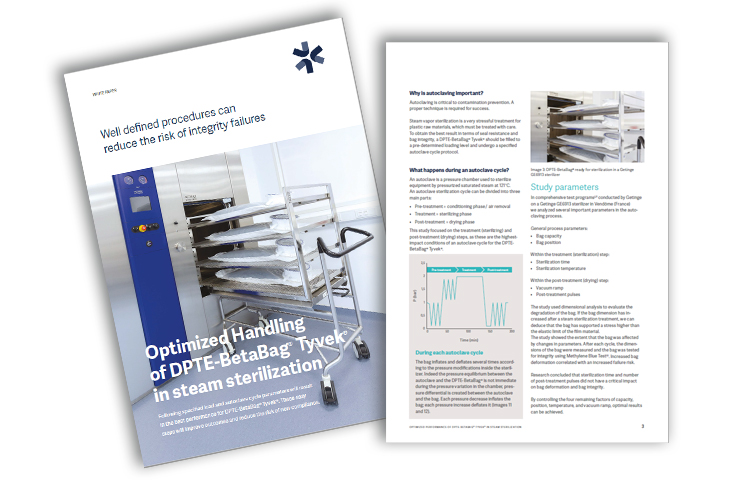
Seguendo i parametri specificati di carico e di ciclo in autoclave si otterranno le prestazioni ottimali della sacca DPTE-BetaBag® Tyvek®. Queste semplici indicazioni consentono di ottenere risultati migliori e di ridurre il rischio di danneggiamento della sacca.
Scoprite come ottimizzare le prestazioni della sacca DPTE-BetaBag® Tyvek® adottando procedure appropriate.