Ensuring contamination-free and scalable processes while fulfilling the strictest compliance requirements
As a partner in pharmaceutical production, Getinge’s portfolio of biopharmaceutical resources meets our customers’ unique challenges and strict compliance requirements while achieving high performance, maximum productivity and streamlined processes. We produce GMP washers, sterilizers, closure processing systems, isolators, sterile transfer systems and bioreactors systems to meet each facility’s specific needs.
Discover how Getinge can support in contamination prevention and upstream bioprocessing for your specific application within the biopharmaceutical production space.
We support every step of your journey
From Science to Life
We help scientists and engineers move from idea to innovation.
From threat to cure. From science to life.
By leveraging our deep application know-how and global footprint, Getinge partners with scientists and engineers to develop and manufacture better pharmaceuticals.
We focus on contamination prevention and upstream bioprocessing to provide tailored, efficient and compliant solutions to our customers and partners who are dedicated to prevent, mitigate and cure diseases - saving lives.
Striving for the highest quality outcome from production processes
Biopharmaceutical production facilities are acutely concerned with maximizing uptime and performance while safeguarding against microbial and particulate contamination.
To ensure safety, all biopharmaceutical production facilities must comply with strict regulations. These include Good Manufacturing Practices (cGMP) associated with production of the finished product, and Good Laboratory Practices (cGLP) associated with quality testing related to the product. Each process and cycle must follow validated customer requirements to deliver stable and repeatable results in the shortest time and at a minimum cost.
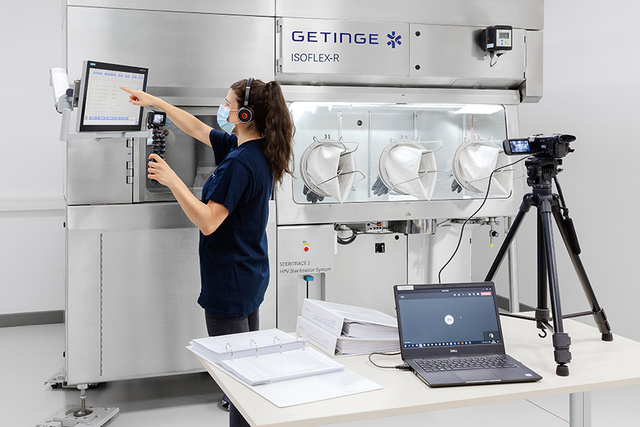
Remote Factory Acceptance Tests (FAT)
To support our customers we use remote FAT as an alternative approach to performing Factory Acceptance Tests.
Complementary to our physical Factory Acceptance Tests, we offer remote FAT to continue to support you even in times of (travel) restrictions.
Solutions tailored to your every need
We design and provide tailored, efficient, and compliant solutions based on our extensive portfolio and experience from +25,000 customers worldwide.
Worldwide presence and experience
Getinge’s worldwide reach, +10,000 employees, and extensive installed base in +135 countries give us the ability to support you anywhere in the world.
A century of application know-how
By leveraging our deep application know-how and global footprint, we partner with scientists and engineers to develop and manufacture better pharmaceuticals.
Our Service Team is always by your side
With our own Service Team by your side, you are ready to meet the requirements of accrediting organizations and government regulatory agencies.
Explore our products
Find the right products and solutions for you